LA CARTA
LE MATERIE PRIME, I PROCESSI PRODUTTIVI E LE TIPOLOGIE
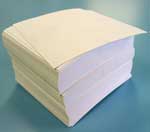
Le materie prime della carta
Le fibre del cotone, del lino e della canapa, che contengono cellulosa in altissima percentuale, costituirono per lungo tempo, fino alla metà dell'Ottocento, le materie prime per la fabbricazione della carta.
Ad esse si sostituirono, rivoluzionando il sistema produttivo, la pasta di legno (o cellulosa) ottenuta da diversi alberi (quali l'abete, il pino, la betulla, il pioppo) o, in misura minore, la paglia di juta o la canna.
Le moderne cartiere, dotate di grandi impianti, possono fabbricare qualsiasi tipo di carta, ma generalmente si specializzano nella produzione di alcuni tipi, che vengono ottenuti sfruttando al meglio le proprietà delle materie prime.
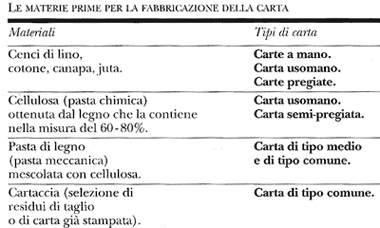
Le materie prime non sono però sufficienti: esse costituiscono solo la parte fibrosa della carta, alla quale devono essere aggiunte le materie collanti, quelle coloranti, e sostanze speciali per diminuirne la trasparenza.
Le lavorazioni che formano il ciclo completo della fabbricazione della carta sono: la preparazione delle materie prime (impasto), la lavorazione dell'impasto e la preparazione del foglio.
Le materie prime sono sottoposte ad operazioni preliminari che disintegrano i tessuti e isolano le fibre riducendole ad una massa fibrosa che prende il nome di pasta.
Le materie prime per la produzione della carta
La carta è un prodotto costituito essenzialmente da fibre vegetali e sostanze di carica minerali inerti.
La diversa combinazione delle fibre, lunghe o corte, delignificate o contenenti ancora lignina, costituisce la differenza macroscopica fra i diversi tipi di carte o cartoni che si otterranno.
Non va dimenticata comunque l'importanza delle cariche minerali che, pur non concorrendo a conferire resistenza al foglio di carta, ne costituiscono sino al 50% in peso (carte patinate), conferendo alla carta maggior lucentezza, brillantezza e stampabilità.
La classificazione
La distinzione più elementare è quella in:
• fibre lunghe, provenienti in massima parte da legni di
resinoso (pino, abete, larice);
• fibre corte, provenienti da legni di latifoglia (faggio, betulle, eucaliptus, pioppo).
Le sostanze minerali di carica più usate sono:
• carbonato di calcio, ricavato macinando finissimamente scarti della lavorazione o dell'estrazione del marmo;
• caolino, proveniente da cave;
• talco, anch'esso di cava.
Le fibre vegetali
Le fibre vegetali provengono in massima parte dal legno, anche se possono essere ricavate da piante annuali quali la paglia di grano o di riso, le canne, lo sparto, la canapa, il lino, il kenaf, ecc.
L'utilizzo industriale di queste piante è oggi invece oggetto di studio e di ricerca nonostante fosse stato praticamente abbandonato per via delle caratteristiche scarsamente "industriali" di estrema stagionalità e per la difficoltà nella depurazione delle acque reflue.
Per produrre paste cartarie si utilizza quasi esclusivamente legname di recupero ed a basso costo, cioè:
• scarti di altre produzioni quali segherie, fabbriche di imballaggi o mobili;
• tronchi di piccola pezzatura e comunque non utilizzabili per lavorazioni qualitativamente superiori.
Per quanto concerne la parte di legname, quantitativamente meno consistente, che proviene dalle foreste, si tratta sempre o dell'utilizzo di sottoprodotti (alberi non adatti alla segagione, cime di piante più grandi, ecc.) oppure proveniente da piantagioni di alberi a rapida crescita (6-8 anni) messi a dimora proprio ad uso industriale.
A tale proposito è opportuno ricordare che le importantissime funzioni di scambio e di trasformazione (da anidride carbonica ad ossigeno) svolte dalle foreste giovani in accrescimento non sono nemmeno paragonabili a quelle di una foresta matura che, avendo rallentato il ciclo vitale, ha un rapporto di scambio (anidride carbonica-ossigeno) decisamente più limitato e tendente al pareggio tra l'ossigeno consumato e quello prodotto.
Le fibre di aghifoglia
La lamella mediana è essenzialmente costituita da lignina, sostanza amorfa e rigida che agisce da collante tra le varie fibre.
Procedendo dall'esterno verso il lume della fibra, la lignina va calando progressivamente sino a sparire praticamente verso la parete interna.
La cellulosa ha un andamento complementare alla lignina e va progressivamente calando dal lume all'esterno sino a scomparire praticamente nella parete primaria.
Possiamo immaginare la fibra come una spagnoletta, i cui fili esterni siano affogati in una gran massa di lignina, nella quale le incrostazioni diminuiscano sempre di più, a mano a mano che si procede verso l'anima, sino ad incontrare i fili che ne sono completamente privi.
Il filo incrostato si presenta duro e rigido, mentre quello pulito è flessibile e morbido; allo stesso modo le fibre molto lignificate si presentano rigide e dure (paste legno da sfibratore o termomeccaniche), mentre le fibre delignificate sono flessibili e morbide (cellulose bianchite).
Lo spessore della parete cellulare influenza la flessibilità della fibra e la sua propensione a presentarsi con aspetto nastriforme.
La fibra a parete cellulare più sottile:
• assume più facilmente un aspetto nastriforme;
• crea superfici di contatto maggiori con le altre fibre;
• riduce i volumi liberi tra fibra e fibra.
La fibra a parete cellulare più spessa:
• assume di preferenza aspetto tubuliforme;
• è più rigida;
• permette superfici di contatto minori con le altre fibre;
• aumenta i volumi liberi tra fibra e fibra.
Perciò da impasti contenenti in prevalenza fibre a pareti sottili dovremo aspettarci carte più dense, più sottili, più resistenti alla trazione, più trasparenti.
Da impasti contenenti in prevalenza fibre a pareti spesse dovremo aspettarci carte più voluminose, meno resistenti alla trazione ed alla piegatura, più resistenti alla lacerazione, più opache. Anche da fibre molto lignificate (paste legno) dovremo aspettarci carte più voluminose ed opache, ma meno resistenti e più fragili in piega.
aaa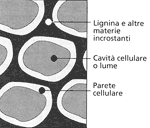
la cellulosa è il principale costituente dei tessuti vegetali, a destra la rappresentazione schematica di alcune fibre avvolte in uno strato di sostanze incrostanti.
La lignina
Il legno è costituito da fibre di cellulosa, vasi e lignina.
Quest'ultima, essendo il collante naturale che tiene unite le fibre, è la sostanza sulla quale si deve agire per separare le fibre da utilizzare per scopi cartari.
Il diverso modo di affrontare industrialmente la lignina e quindi di separare le fibre vegetali dà luogo alla distinzione fra i tipi di fibre cartarie (paste cantare):
• cellulose
• paste semichimiche;
• paste chemitermomeccaniche o chemimeccaniche;
• paste meccaniche.
La produzione delle cellulose
Si possono avere cellulose provenienti da conifere (fibra lunga) o da latifoglia (fibra corta).
Per produrle, il legno, scortecciato e ridotto in pezzetti (chips) per facilitare l'impregnazione, viene sottoposto ad un attacco di sostanze chimiche:
• in ambiente alcalino (idrato di sodio): per ottenere cellulosa al solfato o Kraft (dal tedesco forte) con elevate caratteristiche meccaniche e quindi adatte all'impiego nella fabbricazione degli strati esterni del cartone ondulato, nelle carte da imballo e comunque in tutti i tipi di carta in cui è necessaria una buona resistenza;
• in ambiente acido (solfito): per ottenere cellulose dette al solfito. Tale cottura viene fatta con immissione di vapore ad alta temperatura, in modo da sciogliere tutta la lignina per via chimica e liberare così le fibre di cellulosa con un modestissimo lavoro meccanico tramite raffinatori a disco.
La raffinazione delle cellulose
La raffinazione è un processo duplice di compressione e di sfregamento cui sono assoggettate le fibre che, così elementarizzate, vengono poi lavate, assortite per eliminare eventuali fasci di fibre incotte od altre impurità e quindi convogliate nelle torri di imbianchimento dove, tramite processo di ossidazione con cloro o più recentemente, con acqua ossigenata, le fibre sono sbiancate per essere utilizzate in carte bianche.
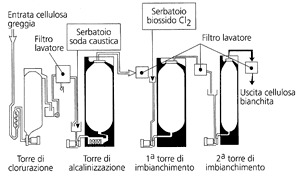
torri di imbiancamento
Il liscivio di cottura viene concentrato per recuperare i prodotti chimici in esso disciolti e la lignina che sotto forma di lignin solfonato è utilizzata anche come collante per la produzione di pannelli truciolari.
Le acque reflue sono depurate tramite depuratore anaerobico o bruciate per produrre vapore nel caso la lignina non sia stata prima estratta.
La resa in fibra delle cellulose, fatto 100 un kg di legno secco, è del 40-45% .
Le caratteristiche cartarie della cellulosa sono ottime dal punto di vista qualitativo, sia come resistenze meccaniche che come grado di purezza e di bianco raggiungibile.
Le carte di pura cellulosa sono quasi illimitatamente durevoli nel tempo e, non contenendo lignina, ingialliscono in modo trascurabile.
Le paste semichimiche
Sono prodotte partendo da chips prevalentemente di latifoglia (faggio e pioppo) ed il ciclo produttivo non si discosta molto da quello descritto per la produzione di cellulosa.
La differenza fondamentale sta nel fatto che la lignina e le sostanze incrostanti non vengono completamente sciolte in quanto l'attacco chimico con solfito di sodio, la cottura, è solo parziale; la resa, partendo dal kg di legno secco, si aggira sul 60% e la fibra di cellulosa è ancora parzialmente lignificata.
Le paste semichimiche hanno caratteristiche qualitative intermedie e non ben definite fra quelle delle cellulose (paste chimiche) e quelle delle paste ad alta resa (paste meccaniche, chemitermomeccaniche e chemimeccaniche), se consideriamo anche gli alti costi di produzione e di depurazione in relazione alla bassa resa capiamo perché si sta gradualmente abbandonando questo metodo produttivo .
Le paste semichimiche trovano comunque il loro impiego nella produzione di carta da giornale, da stampa, nel cartone ondulato, ecc.
Le paste C.T.M.P. (chemistermomeccaniche) e C.M.P. (chemimeccaniche)
Come le altre paste cartarie, le paste chemitermomeccaniche e chemimeccaniche derivano il nome dal processo industriale utilizzato per ricavarle e quindi, ancora una volta, dalla metodologia utilizzata nel trattare la lignina e le sostanze incrostanti che cementano le varie fibre tra di loro e danno corpo e rigidità al contesto legnoso.
Esse fanno parte delle cosiddette paste ad alta resa, questa infatti è dell'85-90% per kg di legno secco: la lignina viene semplicemente ammorbidita attraverso un blando attacco termo-chimico o solo chimico (senza vapore aggiunto) e quindi lasciata in gran parte a ricoprire la fibra di cellulosa.
Tale metodo di produzione prese piede a partire degli anni '60 e si è dimostrato assai confacente sia alle esigenze specificatamente cartarie che alle ovvie necessità di economicità produttiva; il risparmio si realizza infatti sotto diversi profili: minor costo della materia prima (legno meno pregiato), minor impiego di energia elettrica, costi inferiori di depurazione, vantaggi dal punto di vista della tutela ecologica.
Il pioppo, anche di provenienza nazionale, è l'essenza più usata ed apprezzata per produrre C.T.M.P. o C.M.P. ma viene impiegato anche l'abete, gli scarti delle lavorazioni del compensato e delle segherie sono la base per la produzione di queste paste.
Anche questo processo produttivo parte dai chips che, impregnati ad una temperatura inferiore ai 100 ºC con soda caustica per ammorbidire la lignina e perossido di idrogeno (acqua ossigenata) per la sbianca, vengono convogliati in raffinatori a disco allo scopo di elementarizzare le fibre per via meccanica.
la raffinazione
Il raffinatore a dischi è costituito essenzialmente da due dischi metallici posti uno di fronte all'altro, le cui superfici contrapposte sono munite di scanalature dirette verso l'esterno, con dimensioni e forma variabile a seconda dello stadio/grado di raffinazione.
Un disco è fisso, l'altro gira velocemente e può essere allontanato od avvicinato all'altro, all'interno delle due piastre viene forzata la sospensione di legno impregnato e acqua.
Questa, spinta dall'azione del disco rotante e lanciata verso la periferia dalla forza centrifuga, passa attraverso lo spazio esistente tra le scanalature subendo un'azione meccanica di disintegrazione e raffinazione.
Gli altri passaggi
I passaggi successivi consistono nell'assortitura, per scartare e rilavorare fascetti (schegge) di fibre che non si fossero ben aperti nella prima fase di raffinazione ed eventualmente un altro stadio di sbianca al perossido con relativo lavaggio della pasta.
L'operazione di sbianca prevede che la fibra stazioni per un certo periodo all'interno di una tina in una soluzione ricca di acqua ossigenata in base alcalina ed alla temperatura di circa 50-60 ºC, l'acqua ossigenata, svolgendosi in ossigeno per effetto del pH basico, ossida i legami cromofori del legno sbiancandolo.
Le acque reflue
Le acque reflue vengono trattate con un depuratore biologico allo scopo di renderle idonee allo scarico in fognatura o in acque superficiali.
La funzione del depuratore biologico è quella di riprodurre, artificialmente ed in un tempo molto più breve, quella attività di riossigenazione dell'acqua scaricata che in natura necessiterebbe almeno di diverse settimane; l'acqua scaricata alla fine del ciclo produttivo è infatti carica di mucillagini del legno, micro fibre, linfa e zuccheri che vengono espressi in B.O.D. (biological oxigen demand) o C.O.D. (chemical oxigen demand) e che significano carenza di ossigeno nell'effluente.
L'utilizzo e problematiche
Le paste chemimeccaniche o chemitermomeccaniche sono utilizzate per la produzione di quasi tutti i tipi di carta e cartoni, dal tissue (fazzolettini igienici, asciugatutto, tovaglioli, ecc.) alle carte patinate.
Le buone caratteristiche meccaniche (lunghezza di rottura, resistenza alla lacerazione) decisamente elevate per paste ad alta resa, ne consentono impieghi anche massicci.
È opportuno, in questo contesto, aprire una parentesi e sottolineare che, in un Paese come il nostro, notoriamente deficitario di materia prima legnosa (il legno costituisce la seconda voce di importazione dopo la carne), il pioppo è l'unico legno a rapido accrescimento (6-8 anni per la maturazione completa) disponibile in quantità discreta.
Di più, in Italia e soprattutto nella pianura padana, da oltre 100 anni la coltivazione del pioppo fa parte della cultura e della tradizione delle popolazioni rivierasche del Po.
Da sempre questa materia prima rapidamente rinnovabile è utilizzata al 100% dalla base sino ai rami, corteccia compresa.
Il tronco commercialmente più pregiato (trancia), dalla base sino a 20 cm di diametro è utilizzato per produrre compensato, segati, paglia di legno e persino cappelli.
Da 20 cm sino a 10 cm di diametro è utilizzabile per produrre segati o fibre per carta.
Da 10 cm sino a 4 cm di diametro è utilizzato per produrre pannelli truciolari.
La corteccia è utilizzabile come ammendante organico in agricoltura o da bruciare per produrre energia o vapore.
Per continuare con le note di carattere generale, è anche opportuno soffermarsi un momento sull'importanza che ha l'acqua nel ciclo produttivo il cui output finale è la carta; sia le aziende che trasformano legno in paste cartarie che le stesse cartiere necessitano di un massiccio impiego di acqua.
L'acqua è materia prima, vettore, serve nei lavaggi, per diluire la concentrazione di fibre, e resta, in percentuali diverse, nei fogli pressati delle paste e anche nella carta che, non dimentichiamo, è un foglio di natura igroscopica.
La funzione fondamentale dell'acqua ha fatto sì che le cartiere storicamente sorgessero in prossimità di fiumi e torrenti e che oggi siano le prime a promuovere ed incentivare tutto un filone di studi e ricerche volto al risparmio idrico.
Le nuove tecnologie degli impianti di produzione, l'installazione in ogni azienda di imponenti depuratori ed una più consapevole cultura ecologica di tutti gli operatori del settore hanno reso possibile una drastica riduzione della quantità di acqua necessaria per la produzione di carta e paste cartarie, nel caso della C.M.P., per esempio, l'impiego di acqua per la fabbricazione di un chilogrammo di pasta è passato dai circa 12 agli odierni 7-8 litri.
Le paste meccaniche
Il metodo più tradizionale e più semplice per produrre paste cartarie, è quello meccanico da sfibratore.
Anche in questo caso si parla di paste ad alta resa, sino al 90-95% che si ottengono sfibrando il legno esclusivamente per via meccanica.
La materia prima di partenza può quindi essere il solo tronchetto di legno (pioppo o abete) che dopo la scortecciatura viene pressato, in presenza di acqua, contro una mola rotante ed abrasiva.
La pasta ottenuta deve essere assortita e le schegge od i fascetti di fibre sono rilavorati in un raffinatore a dischi.
L'ultima fase di produzione consiste nella sbianca con perossido di idrogeno (H202) ed anche in questo caso le acque reflue sono inviate ad un depuratore biologico.
L'aumento della velocità delle macchine continue da carta e da stampa e la generale diminuzione delle grammature dettata da esigenze di economicità, hanno portato ad un rallentamento nell'impiego delle paste meccaniche e ad una loro graduale sostituzione con impasti cartari più resistenti.
Le migliori caratteristiche di questo prodotto sono infatti da ricercare nella buona stampabilità e voluminosità, non in quelle meccaniche di lacerazione e lunghezza di rottura poiché è lo stesso metodo produttivo che, elementarizzando le fibre esclusivamente per via meccanica, ne lacera, accorciandole, una grande quantità.
Le materie prime non tradizionali
Il sole è la migliore fonte di energia a disposizione dell'umanità. Il processo della fotosintesi clorofilliana è il migliore produttore di cellulosa e di amido ed il più efficace accumulatore di energia.
Bruciando le sostanze vegetali, si spezzetta la cellulosa, l'amido e gli zuccheri ottenendo in cambio anidride carbonica che il processo alla clorofilla può rapidamente ritrasformare con l'aiuto del sole in sostanze vegetali di rapida crescita.
Le attuali materie prime alternative o integrative della carta e del cartone sono a base di sostanze cellulosiche fibrose storicamente già ben collaudate e conosciute.
Anticamente in Europa la carta era prodotta solo con stracci.
Si utilizzavano infatti i ritagli di vestiti e tessuti usati, i cordami delle navi, i sacchi usati.
Le fibre di canapa e lino erano le materie prime usate per la produzione di carta; l'impiego della fibra di cotone avviene più tardi, dopo la scoperta dell'America.
Nella metà del secolo scorso fu inventata l'estrazione delle fibre cellulosiche dagli alberi. Antonio Meucci, l'inventore oggi riabilitato del telefono, da buon cartaio nei suoi brevetti americani precorre la strada della cellulosa ottenuta da alberi con cotture sia acide che alcaline aventi lo scopo di ammorbidire e disciogliere gli incrostanti cementanti (lignina) esistenti tra le fibre cellulosiche del legno.
Oggi, ad un secolo di distanza, si ha l'impressione che la carta sia ottenibile solo dagli alberi quali le conifere (abete e pini) e le latifoglie (eucalipto, betulla e pioppo).
Le erbacee e le pianti annuali
Nel contempo, oggi, grazie alle moderne tecnologie (biogenetica, biochimica, termodinamica e tecnologie ambientali), si riscoprono le erbacee e le piante annuali:
• le erbacee, quali la paglia, i residui delle graminacee (mais, frumento e riso) e i residui delle lavorazioni agro-alimentari, quali la canna e la barbabietola da zucchero oltre che i residui della spremitura degli agrumi (arance e limoni) e gli esuberi marini quali le alghe raccolte nella laguna di Venezia sono impiegabili nella produzione di carte di elevato pregio.
Queste materie prime sono ancora in fase di sperimentazione: il loro costo è per il momento più elevato rispetto alla tradizionale cellulosa:
• le piante annuali, quali il kenaf, il sorgo, il cotone, il lino e molte altre a veloce rinnovabilità e ad altissima resa;
• con la paglia dei cereali (riso, frumento, orzo, ecc.) in Cina si producono fibre cellulosiche;
• gli steli della canna da zucchero (bagasso) nell'America Centrale sono trasformati in carta;
• il sorgo, la manioca, il miscanto, il cotone ed il lino, sono tra i vegetali ad alta resa per ettaro ai fini della coltivazione e talune specie hanno anche una buona resa in paste da carta.
Queste fibre annuali dovrebbero entrare con più forza nell'uso cartario anche tramite apposita legislazione, poiché trattandosi di fibre a ciclo di accrescimento annuale possono ridurre mediamente fino ad un 20% l'uso delle cellulose ricavate da essenze arboree.
Le materie di recupero
L'industria cartaria italiana utilizza in misura crescente fibre secondarie - o di recupero - assicurate dal riciclo, come materia prima, di prodotti cartari usati o comunque usciti dal loro ciclo di uso.
Il termine più comunemente usato per tali fibre è carta da macero (recovered o waste paper in inglese); da evitare è invece quello di carta straccia.
Il riciclaggio delle fibre può avvenire per un numero limitato di volte - da 5 a 7 - tenuto conto del progressivo deterioramento delle prestazioni, determinato dal riciclo.
Le qualità inferiori sono prevalentemente utilizzate nella produzione di cartone e carte per ondulatori, nella cui produzione possono peraltro essere utilizzate anche quote significative di macero di qualità più pregiate.
Queste ultime sono maggiormente utilizzate, previa disinchiostrazione.
Sotto il profilo delle fonti di raccolta il macero si distingue in:
• macero da raccolta industriale e commerciale costituito dai rifili di cartotecnica, casse di cartone ondulato, rese di quotidiani e periodici, tabulati, ecc.
Questo macero è localizzato presso industrie cartotecniche ed editoriali, uffici, grandi magazzini, è raccolto da recuperatori professionali e quindi selezionato e imballato prima di essere fornito alle cartiere per rientrare nel ciclo produttivo;
• macero domestico proveniente da raccolta differenziata, contenente prodotti cartari detenuti nelle abitazioni e nei piccoli negozi e uffici.
Questo macero, prevalentemente costituito da cartaccia mista e giornalame, deve essere isolato dai rifiuti solidi urbani all'origine, cioè prima che la carta sia mescolata con altri materiali che, inquinandola, la rendano inutilizzabile.
Ciò presuppone l'organizzazione, da parte dei comuni, della raccolta differenziata; il macero che ne deriva può essere utilizzato come tale da alcune cartiere che procedono all'interno dei loro impianti all'eliminazione delle impurità mentre in altri casi è necessario l'intervento di operatori ambientali per la selezione e l'imballaggio.
La produzione
Con diversi procedimenti si possono ottenere impasti diversi per diversi tipi di carta, e cioè: pasta di stracci, cellulosa, cellulosa di paglia, pasta di legno, pasta di cartaccia, ecc.
I vari impasti, a seconda delle destinazioni d'uso, subiscono altre lavorazioni. Le principali sono:
la raffinazione il legamento delle fibre
la collatura l'aggiunta di sostanze collanti per impedire lo spandimento dell'inchiostro sul foglio,
la colorazione con sostanze minerali organiche.
Il foglio può essere fabbricato a mano o a macchina.
La fabbricazione a mano si svolge con un procedimento pressoché identico a quello di un tempo e serve a produrre piccoli quantitativi di carta pregiata, utilizzando soprattutto pasta di straccci
La fabbricazione a macchina può essere effettuata con macchine continue in piano o in tondo che producono cioè fogli o nastri di carta.
Negli stabilimenti più moderni sono in funzione macchine in tondo.
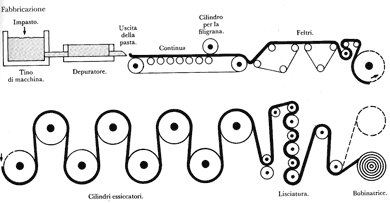
schema di fabbricazione della carta
Le caratteristiche generali
Descrivere in poche righe il complesso processo di fabbricazione della carta è impresa impossibile se il tutto non viene generalizzato ed estremamente semplificato; ma nell'eccessiva semplificazione si nasconde sempre il pericolo di banalizzare l'argomento senza coglierne più di tanto l'essenza.
Innanzitutto ogni azione (processo) che genera un risultato o un prodotto si basa su 4 elementi fondamentali:
• Chi la compie;
• Gli strumenti necessari per compierla;
• Gli ingredienti o le sostanze (anche quella grigia) che vengono manipolate;
• I soldi necessari per procurarsi il tutto.
Ogni processo inoltre, sia esso semplice o complicatissimo, consta di:
• una fase di studio (ricetta o formulazione del progetto);
• una fase preparatoria (miscelazione ingredienti o materie
Aprime ed adeguamento e scelta dei mezzi o degli impianti necessari);
• una fase produttiva;
• una fase di finitura e di allestimento;
• la realizzazione finale;
• i controlli relativi ad ogni fase.
Anche la fabbricazione della carta è riconducibile perciò ad uno schema semplice nelle sue linee generali.
La complessità nasce dal numero delle fasi che compongono il processo, dagli impianti, specifici per ogni fase, dalle dimensioni in gioco e dalla necessità di amalgamare correttamente il tutto.
Il processo produttivo della carta
la produzione della carta è caratterizzata da queste fasi:
• la preparazione dell'impasto
• lo spappolamento e la raffinazione
• il testa macchina e la preparazione del foglio
• la tavola piana
• le presse umide
• la secchiera
• la patinatura
• l' allestimento
La preparazione dell' impasto
La formulazione dell'impasto nasce avendo la conoscenza di alcuni aspetti fondamentali:
• le caratteristiche del prodotto desiderato
• le materie prime che rendono possibile l'ottenimento di
a queste caratteristiche
• la consapevolezza di possedere un impianto idoneo a sviluppare
a e realizzare queste caratteristiche
• la consapevolezza di essere in grado di gestire il tutto in modo corretto
La formula o ricetta di impasto elenca sia il tipo che le quantità di
materie prime previste; generalizzandola si può così schematizzare, anche
se in modo incompleto:
MATERIE PRIME |
TIPO DI PASTA |
TIPO DI FIBRA |
FONTE |
Fibrose |
Chimica |
Lunga (aghifoglie) |
Abete |
Fibrose |
Chimica |
Lunga (aghifoglie) |
Pino silvestre |
Fibrose |
Chimica |
Lunga (aghifoglie) |
Pino del sud |
Fibrose |
Chimica |
Corta (latifoglie) |
Pioppo, betulle |
Fibrose |
Chimica |
Corta (latifoglie) |
Eucalipto |
Fibrose |
Chimica |
Corta (latifoglie) |
Faggio |
Fibrose |
Meccanica |
Lunga (aghifoglie) |
Abete |
Fibrose |
Meccanica |
Corta (latifoglie) |
Pioppo |
Fibrose |
C.T.Meccanica |
Lunga (aghifoglie) |
Abete |
Fibrose |
C.T.Meccanica |
Corta |
Aspen |
Fibrose |
Pasta da fibre secondarie |
|
Maceri disinchiostrati |
Non fibrose |
Sostanze di carica |
Caolino |
|
Non fibrose |
Sostanze di carica |
Carbonato di calcio |
|
Non fibrose |
Sostanze di carica |
Solfato di calcio |
|
Non fibrose |
Sostanze di carica |
Talco |
|
Non fibrose |
Sostanze di carica |
Biossido di titanio |
|
Non fibrose |
Collanti |
Per ambiente alcalino |
|
Non fibrose |
Collanti |
Colofonia |
|
Non fibrose |
Allume (policloruro) |
. |
|
Non fibrose |
Ritentivi |
Poliacrilammidi |
|
Non fibrose |
Ritentivi |
Polietilenimmine |
|
Non fibrose |
Ritentivi |
Amidi cationici |
|
Non fibrose |
Coloranti |
|
|
La tabella ha delle lacune, ma dà senz'altro un'idea dei materiali che vengono citati in una formulazione d'impasto.
Spappolamento e raffinazione
Le essenze fibrose previste dalla ricetta d'impasto vengono spappolate in acqua mediante una apposita macchina (Pulper).
Le fibre, per effetto dell'acqua, si rilasciano e si ammorbidiscono diventando pompabili.
Vengono stoccate in tine, in attesa di subire un trattamento atto a sviluppare quelle caratteristiche di resistenza e macchinabilità già insite nei tipi di essenze scelte (raffinazione).
L'impasto raffinato viene quindi dosato assieme ad altri componenti, nelle proporzioni previste dalla ricetta.
Per meglio cogliere il significato del processo di raffinazione occorre però prima conoscere la conformazione delle fibre, perciò illustreremo schematicamente, qui di seguito, la struttura di una fibra di aghifoglia.
La raffinazione
La raffinazione è l'operazione con cui si ottiene dall'impasto fibroso quelle caratteristiche richieste dall'utilizzatore:
• Chi stampa in roto-offsetvorrà una carta resistente alla piega ed al punto metallico, o alla cucitura in genere;
• Chi stampa in offset piano vorrà una carta rigida e altamente macchinabile, ma dimensionalmente stabile ed il più possibile inerte;
• Chi utilizza carte leggere per editoria le vorrà parimenti resistenti alla lacerazione, alla piega, al punto metallico o cucito oltre che sufficientemente chiuse per avere una sufficiente brillantezza di stampa;
• Chi impiega carte porcellanate, o smalti che dir si voglia, vuole carte resistenti e decisamente poco porose, poco permeabili;
• Tutti poi richiedono una opacità elevata e, a livello di desiderio, la massima opacità possibile ed immaginabile;
Una raffinazione mirata e ben condotta, in presenza di strumenti (raffinatori) idonei, consente di sviluppare dalle fibre le caratteristiche richieste e, quando queste caratteristiche sono tra loro in contrasto, di mediare con equilibrio il risultato.
aa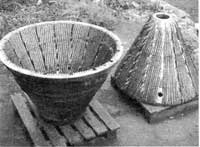
a sinista lo schema di un raffinatore conico, a destra un raffinatore conicop aperto
aaaaaaaaa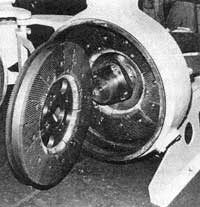
a sinistra lo schema di un raffinatore a dichi, a destra un raffinatore a dischi
La raffinazione sottopone la fibra ad una serie di sbattimenti e compressioni che consentono all'acqua di imbibirne sempre di più le fibrille interne rendendola sempre più plastica; questa aumentata plasticità consente la formazione di un maggior numero di aree di contatto, e quindi di legami, indispensabili per una buona resistenza e formazione del foglio.
La raffinazione, se inidonea o troppo spinta, produce anche altri effetti non sempre desiderabili ed opportuni;(smodata lacerazione della parete, accorciamento esagerato della fibra, eccessiva idratazione).
Sulle fibre di cellulosa la violenza dell'urto delle lame del raffinatore non deve essere tale da devastare la superficie ad ogni colpo; e poiché le caratteristiche morfologiche e chimico-fisiche delle fibre sono peculiarità proprie di ogni tipo di essenza (abete, pino silvestre, pino del sud, pino della costa del pacifico, faggio, eucaliptus, ecc.) si intuisce l'opportunità di raffinarle in modo selettivo (raffinazione separata), per non rovinare una fibra lunga che può darci una carta tenace e porosa, ma rendendole plastiche ed in grado di creare, su tutta la loro integra lunghezza, un numero elevato di legami.
Lo sviluppo di alcune caratteristiche non sempre è in accordo con altre.
Infatti se da un lato aumentare la predisposizione delle fibre a creare più legami e punti di contatto porta a resistenze meccaniche migliori, dall'altro comporta un peggioramento della opacità.
Se si insiste con la raffinazione per esaltare le caratteristiche meccaniche di resistenza alla trazione, accanto a questa dovremo accettare una minor resistenza alla lacerazione.
All'impasto fibroso raffinato vengono aggiunte sostanze che conferiscono al prodotto finito altre caratteristiche:
• la colla e l'allume per dare una certa resistenza alla bagnatura o per regolare un assorbimento eccessivo di inchiostro per scrivere, impedendone il trapasso e la sbavatura;
• le sostanze di carica per conferire alla carta opacità, maggiore levigatura, migliore stampabilità.
Il testa macchia e la formazione del foglio
L'impasto, proveniente dalla tina di miscela e pressoché completo in tutti i suoi componenti, viene inviato al vaschino a livello costante dal quale viene dosato, mediante la valvola della grammatura, nell'aspirazione della pompa di alimentazione (fan pump).
Questa pompa, che pesca dalle acque del sottotela (torre raccolta sottotela), diluisce e miscela la pasta prelevata dal vaschino e la porta in cassa d'afflusso facendola prima passare attraverso un impianto di epurazione ed un assortitore (screen).
La cassa d'afflusso ha il compito di distribuire uniformemente sulla tela di formazione l'impasto diluito.
Il complesso fan Pump - epurazione - screen - cassa d'afflusso - torre acque è chiamato giro corto di macchina o testa macchina.
La tela di formazione e la tavola piana, che è composta da vari elementi drenanti (foils, vacufoils, casse aspiranti), consentono di drenare l'acqua trattenendo le fibre ed i componenti dell'impasto. Alla fine della tavola piana il foglio umido è formato.
La prima e la seconda pressa (e, dove esiste, anche la terza) tolgono ulteriore acqua e rendono più consistente e resistente il foglio.
La batteria essicatrice o seccheria consente di asciugarlo completamente.
Abbiamo già detto dell'importanza del ruolo svolto dall'acqua nella fabbricazione della carta.
L'acqua imbeve e idrata le fibre, le rende flessibili e raffinabili, consente di miscelare uniformemente con l'impasto fibroso gli altri componenti, rendendo il tutto pompabile.
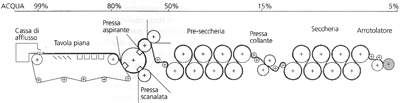
schema di macchina continua per la produzione della carta,
la prima maccina continua fu ideata nel 1799 da Nicolas Louis Robert
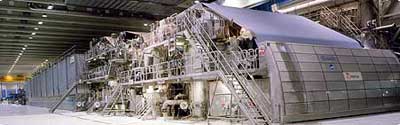
macchina per la produzione della carta
Diamo un'idea della presenza dell'acqua lungo il ciclo produttivo dal pulper al pope con qualche indicazione di densità dell'impasto espressa in percentuale. (Una densità del 3% starà ad indicare che su 100 kg di impasto avrò 3 kg di solido e 97 kg.litri di acqua).
densità
Pulper
|
normalmente da 5% a 14% in funzione dell'impianto (a bassa, a media, ad alta densità) |
Trasferimento dal pulper |
da 4% a 8% |
Raffinazione |
Normalmente da 3,5% a 4% |
Vaschino a livello costante |
Normalmente da 3% a 3,5% |
Epurazione screen, cassa afflusso |
normalmente da 0,6% a 1,1%in funzione della grammatura e del tipo di carta |
Prima delle casse aspiranti della tela |
circa il 3% - 5% per tavole piane con ballerino |
All'uscita della tela |
normalmente da 16% a 20% |
All'uscita della 1^ pressa |
normalmente da 33% a 40% (in funzione anche dei tipi di carta e della velocità di produzione) |
All'uscita della 2^ pressa |
normalmente da 42% a 47% |
Al pope |
di norma 93% - 94% |
La tavola piana
Su di essa inizia un drenaggio graduale, dapprima il più possibile dolce e controllato, mediante i foils.
Questi elementi drenanti, posti dopo la cassa d'afflusso, hanno la funzione di tenere "mossa" la pasta sulla tela, di "richiamare" nelle maglie della tela e sotto di essa l'acqua dell'impasto, di "togliere" con la punta (naso) l'acqua richiamata nelle e sotto le maglie dal foil precedente.
Dopo il primo tratto della tavola piana la leggera depressione creata dai foils non è più sufficiente a togliere l'acqua ed è necessario ricorrere ad elementi drenanti (vacufoils, casse umide, casse aspiranti, cilindro aspirante) che, creando un vuoto sempre più alto sotto la tela, costringono l'acqua a lasciare la fibra.
Le presse umide
All'uscita del cilindro aspirante il secco della pasta è compreso tra il 16% ed il 20%.
Per togliere ancora acqua si deve ricorrere ad una "spremitura", ottenuta esercitando sul foglio umido una fortissima pressione (presse umide).
Ma l'acqua "spremuta", se non trovasse sfogo attraverso un corpo permeabile soffice e resiliente, eserciterebbe sul foglio una pressione idraulica tale da provocarne la rottura (franatura).
Il feltro umido quindi, oltre alla funzione di sostegno, funge anche da ricettore d'acqua e da tutore della integrità del foglio umido.
La seccheria
All'uscita delle presse umide il foglio, in funzione del tipo di presse a disposizione e dell'impasto, può avere un secco generalmente compreso tra il 42% e il 50%.
Per andare oltre il 50%, che è attualmente un valore limite raro e di tutto rispetto, bisogna togliere l'acqua con un altro sistema.
Sino ad oggi non si è trovato di meglio che eliminarla per evaporazione, appoggiando e premendo il foglio, mediante una tela ad anello chiuso (tela essicattice), su delle superfici riscaldate (cilindri essicatori).
Anche in questo caso l'acqua, evaporata attraverso la maglia della tela essicatrice, viene estratta ed espulsa, dopo averne sfruttato la temperatura con degli scambiatori.
Delle soffianti di aria calda provvedono ad eliminare ogni residuo di umidità dalle maglie delle tele che ritornano, asciutte e condizionate, a svolgere la loro funzione.
La patinatura
L'idea di coprire la superficie di un foglio di carta con dei pigmenti minerali di ridotte dimensioni particellari per ottenere una miglior brillantezza ed uniformità di stampa, un bianco più elevato, una lisciatura superiore ed una possibilità di "lucidatura" altrimenti irraggiungibile, nasce e trova applicazione in Italia intorno agli anni '20.
È indubbiamente un'idea vincente, con risvolti economici positivi e, all'inizio, non completamente prevedibili, tanto che ai nostri giorni poche sono le cartiere che non adottano questa tecnologia.
L'operazione di stendere con uniformità, sulla superficie di un foglio, una miscela di pigmenti (patina) è chiamata " patinatura", e "patinatrici" sono dette le macchine che la rendono possibile.
È abbastanza intuibile che uno strato di soli pigmenti, una volta asciutti non rimarrebbe attaccato alla superficie del foglio e basterebbe una qualsiasi azione meccanica, uno sfregamento, una piegatura, una stropicciatura, per staccarlo a pezzi o sotto forma di polvere; la carta sarebbe inutilizzabile.
Bisogna, in qualche modo, "legare" tra loro i pigmenti e legare questi alla superficie del foglio ricorrendo all'impiego di sostanze idonee allo scopo, i cosiddetti "leganti".
Volendo quindi meglio definire la patina, diremo che questa è una miscela di pigmenti e leganti, avente un contenuto in solidi ben definito e la tinta desiderata, idonea ad essere uniformemente distribuita sulla superficie di un supporto cartaceo.
Accontentiamoci di questa definizione che, sotto il generico termine "idonea", nasconde problemi di reologia e ritenzione in rapporto alla velocità di applicazione ed al tipo e grammatura di supporto.
aaaa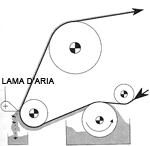
macchine patinatrici, a sinistra a rullo livellatore, a destra a lama d'aria
aaaaa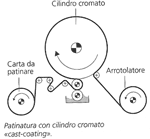
macchine patinatrici, a sinistra a lama meccanica, a destra con cilindro cromato
Al giorno d'oggi, nella maggioranza dei casi, quando si parla di pigmenti si intende parlare di carbonato di calcio e di caolino; qualche cartiera, ma non molte, impiega ancora il bianco-satin mentre sta crescendo l'impiego, nelle carte per rotocalco, del talco.
Un tempo il pigmento principe era il caolino e l'impiego del bianco-satin era più diffuso, ma erano impiegati anche il solfato di bario (bianco-fisso) e la farinafossile.
Il biossido di titanio ha sempre avuto un impiego limitato in applicazioni e tipi di carta particolari.
Agli inizi della patinatura il legante classico era la caseina lattica, sposa ideale del bianco-satin con cui dava patine fluide, microporose e con eccezionali resistenze ad umido.
L'unione con il caolino era invece estremamente "conflittuale" ed originava degli shock reologici con innalzamenti vertiginosi della viscosità tanto che non era eccezionale il verificarsi del bloccaggio delle pale dell'impastatrice per la tenacità del pastone caolino-caseina che si formava.
Un tempo, infatti, si usava preparare la patina partendo dal caolino in polvere ed impastandolo con una soluzione alcalina di cascina in una vera e propria impastatrice, sicché questa somiglianza al mondo dei panettieri e dei pastai, unita al ricettario spesso volutamente misterioso, può essere l'origine del nome "cucina", dato ancor oggi al reparto ove viene preparata la patina.
Ora i leganti principe sono i lattici, soprattutto a base stirene butadiene e/o a base acrilica, seguiti dall'amido e, in misura minore, le proteine vegetali e l'alcool polivinilico. Poiché, quando si parla di patinate, ci si immagina quasi sempre una carta lucida, è interessante sapere che la propensione di una carta patinata a "lucidarsi" è dovuta al tipo di pigmento usato e alle dimensioni delle sue particelle.
Tutto ciò che viene aggiunto ai pigmenti nella preparazione della patina, cioè i leganti, i ritentori d'acqua, i livellanti ed i regolatori di flusso riducono il livello di lucido ottenibile.
È bene inoltre sapere che un pigmento formato da particelle uniformemente molto fini (ad esempio 95% inferiori a 2 micron e 78-80% inferiori a 1 micron) permette di ottenere lucidi più elevati di quelli ottenibili da un pigmento più grossolano.
L'operazione "patinatura" consiste nello spalmare uniformemente sulla superficie del foglio uno strato ben definito di patina; per fare ciò ci si avvale di macchine dette "patinatrici" che, nel tempo, sono andate via via modificandosi pur mantenendo fermi i momenti caratteristici dell'operazione:
l.
l'applicazione, sul foglio, di una quantità esuberante di patina;
2. la sua uniforme distribuzione su tutta la superficie, eliminando l'eccesso;
3. il suo asciugamento;
4. il suo condizionamento ad una ben definita umidità relativa.
La prima patinatrice patinava un solo lato del foglio ed era identificata anche come "patinatrice semplice".
Se si voleva patinare anche l'altro lato si doveva ripassare sulla macchina il foglio monopatinato.
Un cilindro, immerso nella patina contenuta nel calamaio, applicava in modo disuniforme una quantità esuberante di patina sul foglio che, subito dopo, aderiva con il lato non patinato, alla superficie di un cilindro di notevole diametro (tamburo patinatore) e porgeva il lato patinato all'operazione di distribuzione uniforme su tutta la superficie, operazione che veniva effettuata da spazzole, lunghe quanto era largo il foglio, montate a due o a tre su dei telai mobili e regolabili, in modo da poter "premere" più o meno sulla superficie patinata.
I telai, grazie ad una camme, avevano un doppio movimento e facevano compiere alle spazzole delle specie di ellisse, sicché la patina veniva distribuita con spazzolature di senso alternato.
Le spazzole erano rigorosamente di setole di porco, le prime più dure e le successive meno.
Tutte erano mobili, tranne le ultime, che dovevano dare la finitura e che dovevano essere morbidissime (i piumini, rigorosamente di pelo di tasso).
Dopo le spazzole il nastro di carta entrava nel tunnel e "galleggiava" su di un cuscino di aria calda che asciugava e "bloccava" la patina al punto da non "sporcare" il feltro, praticamente il primo ed unico "punto fisso" tra lo svolgitore e l'avvolgitore.
L'asciugamento veniva quindi completato nella cosiddetta "distesa" o "bastoniera", ove un giro di bastoni sosteneva il foglio, appeso come un festone alto 3 metri, mentre da sotto veniva insuffiata aria calda.
Entrare ed aggirarsi tra i festoni (stiamo parlando di percorsi di 20-25 metri per il tunnel e di altrettanti e più per la distesa) dava sempre l'impressione di essere in mezzo a 100 lenzuola stese ad asciugare dopo il bucato.
Nell'ultima parte, prima di venire riavvolta, la carta passava attraverso una specie di sauna ove si riumidificava ad una umidità relativa più consona.
Prima dell'arrotolatore i bastoni, attraverso un percorso alternativo, ritornavano nei paraggi del feltro e riprendevano il nastro per riaccompagnarlo nuovamente lungo tutta la distesa.
Il passo di poco successivo fu la patinatura contemporanea dei due lati del foglio e, nella patinatrice, il tamburo patinatore lasciò il posto alla fila di spazzole inferiori.
E vennero quindi i rullni, che presero il posto delle spazzole e consentivano velocità di produzione più alte, anche se patinare con i rullini dei supporti leggeri non era quasi mai gratificante.
E giungiamo quindi ai nostri giorni, ove la fase di patinatura segue il medesimo procedimento, ma val la pena ricordare che in pochi anni lo sviluppo tecnologico ha permesso di passare dai 20-30-40 metri al minuto delle prime patinatrici a spazzole agli 800-1000-1200-1400 metri al minuto delle attuali patinatrici.
E sugli impianti pilota si toccano già i 2000 metri.
L'allestimento
I clienti, quando ordinano la carta alla cartiera, staccano l'ordine avendo ben presente il lavoro che devono fare e le macchine da stampa che ritengono di utilizzare.
Poiché i clienti sono tanti, i lavori i più disparati, il parco macchine da stampa variato e numericamente assai consistente, si comprende il perché sia difficile semplificare in pochi standard le varie voci (richieste) degli ordini.
Ma alcune standardizzazioni, a livello generale, possono essere fatte:
• carta in rotolo (per stampa in roto-offset o in rotocalco o simili)
• carta in formato (per stampa in offset piano)
L'allestimento delle carte in rotolo avviene servendosi di macchine chiamate "bobinatrici", le quali provvedono a ricavare, partendo dal rotolo a tutta altezza di macchina continua, dei rotoli di altezza inferiore.
Nell'allestimento della carta in formato vengono impie
gate macchine, le "taglierine", che consentono di tagliare e raccogliere in fogli di dimensione voluta la carta avvolta in rotolo.
Il taglio trasversale avviene sotto il "coltello" che, in funzione della grammatura della carta, può tagliare contemporaneamente 3, 4, 5, 6 e fino a 12 fogli sovrapposti.
I fogli tagliati vengono raccolti, alla fine della taglierina, su dei pallets (raccoglifoglio) che, accuratamente protetti da un idoneo avvolgimento (polietilene termoretraibile), prenderanno la strada dei magazzini e, quindi, del cliente cui sono destinati.
La carta tagliata in formato può essere venduta impaccata (a 500, a 250, a 100 fogli in funzione della grammatura) su pallet, in pacchi confezionati con un'apposita carta protettiva (generalmente politenata), oppure "sfusa" su pallet (bandierata).
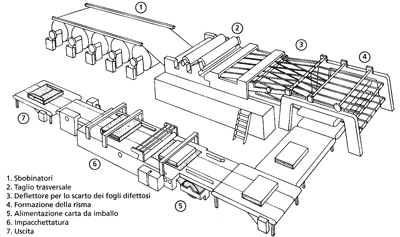
machina per il taglio delle bobine di carta e l' impacchetamento dei fogli
la classificazione delle carte
le categorie
I prodotti cartari si possono suddividere in 6 grandi categorie:
1) carta da stampa
che vengono usate generalmente per giornali e guide telefoniche, per stampa in offset che siano essi depliant, volumi pubblicitari,per rotocalco, per roto-offset e anche per carte speciali (carte geografiche, carta moneta e per assegni)
2) carta da scrivere e per ufficio
sotto questa voce generalmente possiamo trovare la carta per buste, carta per quaderni, carta per disegno, carta per fotocopie, carta per fax, carta da diazotipia, carta carbone e autocopiante
3) carte da imballaggio
possiamo racchiudere qui generalmente la carta kraft, crespata e per sacchetti, carta per alimenti, carta pergamena vegetale, carta uso pergamena, carta pergamino, carte catramate, siliconate, accoppiate con plastica
4) cartoni e cartoncini
cartoni a un getto, cartoni a più strati, cartoni ondulati, carta da onda, cartoni pressati,cartonlegno
5) articoli igienico-sanitari
carta igienica, fazzoletti, tovaglioli e tovaglie, asciugamani,carte per uso medico
6) carta per uso industriale e varie
carta per cavi elettrici e condensatori, ecc.,carta per laminato plastico, carta per sigarette,carta per fotografia, carta da filtro, carta adesiva, carta decorativa, carta da parati
Le carte per uso grafico
Tra i vari tipi di carte e cartoni una posizione di assoluto rilievo è occupata dalle carte grafiche, cioè quelle carte destinate a diventare supporto per la stampa.
Fanno parte di questa categoria le carte usate per produrre quotidiani, settimanali, periodici in genere, libri, pieghevoli, biglietti, carte e buste intestate, calendari e per realizzare tanti altri prodotti stampati.
Ogni stampato ha specifiche richieste:
economicità, minimo spessore, giusto rapporto tra peso e volume, resistenza all'uso, alla luce, al tempo, rigidità, finitura superficiale colore
.
Le carte da stampa si possono classificare a seconda del procedimento di stampa al quale sono destinate:
offset, rotocalco, flessografia, serigrafia.
Le carte destinate alla stampa dovranno inoltre essere adatte alle lavorazioni di post-stampa dette anche di confezione quali:
il taglio, la piegatura, la cordonatura, la cucitura e l'incollaggio.
Le carte per stampa sono fornite in bobine per la stampa in rotative e in formato (fogli) per la stampa con macchine alimentate a fogli.
Nel formato della carta per la stampa con macchine alimentate a fogli,
le bobine prodotte dalla macchina continua saranno tagliate in formato nel reparto allestimento della cartiera stessa,
i formati standard sono il protocollo (64x88) e l'elefante (70x100).
Stampare significa trasferire, mediante pressione, l'inchiostro dalla forma da stampa inchiostrata al supporto. Stampare bene significa trasferire l'inchiostro sul foglio senza deformazioni e alterazioni del segno in modo da ottenere un'impronta nitida, secca e dell'intensità prevista.
Il rapporto tra il supporto e la stampa
Perché ciò avvenga è necessario che mediante la pressione di stampa si riesca ad ottenere un perfetto contatto tra la superficie inchiostrata e il supporto di stampa.
Tenendo conto che la carta normalmente ha un basso coefficiente di comprimibilità, si tende a produrre la carta da stampa con il più alto grado di liscio possibile e ciò, appunto, per facilitare il contatto e quindi il trasferimento.
Le carte da stampa che per esigenze estetiche debbano presentare la superficie ruvida o addirittura marcata o goffrata non potranno essere stampate in rotocalco e in generale nei sistemi a stampa diretta.
Saranno invece stampabili con i procedimenti offset e roto-offset.
I procedimenti offset sono detti a stampa indiretta in quanto la carta non preleva direttamente l'inchiostro dalla forma da stampa inchiostrata, ma lo riceve da un elemento intermedio costituito da una superficie di gomma di opportuna durezza ed elasticità che si adatterà alla superficie del supporto rendendo così possibile un buon trasferimento anche su superfici a basso grado di liscio.
È noto che la stampa di soggetti a colori si ottiene in passaggi successivi depositando sul foglio, ogni volta, uno dei tre colori primari più il nero.
Ciò avviene in macchine costruttivamente molto precise che garantiscono, anche alle attuali elevate velocità di esercizio (15.000 fogli/ora per le macchine a foglio e 50.000 giri-macchina per le rotative), una perfetta sovrapposizione delle immagini monocromatiche costituenti il soggetto finale.
La carta ha un ruolo importante nell'ottenimento di immagini perfettamente giustapposte, indipendentemente dal formato, dallo spessore, dalla velocità di stampa deveessere stabile dal punto di vista dimensionale e non subire alcuna variazione tra la stampa dei vari colori.
A questo scopo è molto importante anche il contenuto igrometrico della carta. La carta lascia la cartiera con un ben preciso contenuto d'acqua in modo che durante il processo di stampa non abbia né a perdere né ad aumentare il contenuto di umidità garantendo così il massimo della stabilità dimensionale.
Caratteristiche della carta da stampa
La carta da stampa ha quindi le seguenti caratteristiche:
1) funzionali al prodotto da ottenere;
2) ottico-estetiche;
3 )di stampabilità;
4) di macchinabilità sia durante la fase di stampa che di allestimento.
Le carte da stampa si possono dividere in due categorie:
1) naturali, cioè a fibra nuda;
2) patinate, cioè con fibra ricoperta.
Le carte naturali
Sono le carte sulla cui superficie non vengono stesi strati per modificare le caratteristiche superficiali.
Sulle carte naturali possono essere effettuati i trattamenti di marcatura e goffratura.
Le carte patinate
Si dicono patinate le carte sulle quali, durante la fabbricazione o in un secondo momento vengono stesi uno o più strati di patina allo scopo di aumentarne il grado di liscio, di lucido, di conferire determinati colori o grado di bianco.
Tutte le carte possono inoltre subire un trattamento finale di lisciatura o di calandratura.
La calandratura aumenta il grado di liscio e conferisce un'elevata lucidità.
La clasificazione delle carte patinate
Le carte patinate si distinguono ancora in:
• Patinatino (LWC): carte di grammatura finale inferiore ai 52 gr/m² con un supporto contenente legno, usate per la produzione di settimanali, cataloghi a distribuzione postale.
• Patinate moderne: carte di grammatura finale tra i 60 gr/m² e i 120 gr/m² con o senza legno usate per produzione di stampati commerciali ed editoriali. Allestimento in bobina e fogli.
• Patinate classiche: carte di grammatura finale tra i 100 e i 240 gr/m² senza legno. Sono usate per stampa editoriale e sono allestite a fogli.
In riferimento alle materie prime impiegate le carte da stampa possono essere di pura cellulosa, o con percentuali variabili di legno e cellulosa.
Un cenno a parte dovrebbe essere dedicato alla carta per quotidiani ottenuta con il processo di riciclo delle fibre cellulosiche delle carte da macero e trattate con tecnologie della disinchiostrazione.
Con la stessa tecnologia vengono prodotte carte utilizzate per la stampa degli elenchi telefonici.
Il seguente specchietto riassume alcune delle caratteristiche alla carta da stampa.
le caratteristiche fondamentali della carta per uso grafico
INCHIOSTRABILITÀ |
EVIDENZIABILITÀ |
MACCHINABILITÀ |
Ricezione e stabilizzazione dell'inchiostro sulla carta |
Grado di bianco |
Resistenza alla trazione |
Trasferibilità dell'inchiostro |
Opacità |
Resistenza alla lavorazione |
Densità della stampa |
Lucido |
Resistenza allo spolvero |
Trapasso dell'inchiostro da stampa |
Nuance |
Resistenza allo strappo |
Contrasti di tinta o liscio |
|
Resistenza alla vescicazione |
Porosità |
|
Resistenza alla delaminazione |
pH superficie |
|
Grammatura e spessore |
|
|
Direzione di fibra |
|
|
Planarità |
|
|
Igroespansività |
Tipologia delle carte grafiche
TIPO DI CARTA |
ALLESTIMENTO |
Carte grafiche naturali senza legno |
In formato e/o in bobina |
Carte grafiche naturali con legno |
In formato e/o in bobina |
Carte grafiche patinate senza legno (classiche - speciali - moderne) |
In formato e/o in bobina |
Carte grafiche patinate con legno (classiche - speciali - moderne) |
In formato e/o in bobina |
Carte grafiche patinatino con legno per rotocalco |
In bobina |
Carte grafiche patinatino con legno per roto-offset |
In bobina |
Le carte a base macero
Da alcuni anni si parla molto di carta riciclata. Il motivo di questo interesse è legato sia all'aspetto ecologico che a quello economico.
Infatti l'uso delle materie seconde (maceri) limita il ricorso alle materie prime vergini e contemporaneamente riduce la quantità di materiali destinati alle discariche con abbattimento dei costi di smaltimento.
Il riciclaggio
Ogni anno vengono avviate alla discarica in Italia oltre 1.000.000 di tonnellate di quotidiani e periodici e circa 100.000 tonnellate di stampati la cui raccolta fornirebbe altrettanta materia prima di qualità alle cartiere italiane.
Il tasso di raccolta italiano è in assoluto il più basso in Europa (28% contro 58% in Germania).
Poiché i materiali cellulosici rappresentano tra il 25 ed il 30% dei rifiuti solidi urbani e tale quota è crescente, le amministrazioni locali sostengono un onere elevatissimo - a carico della collettività - per avviare in discarica tale materiale.
l'importazione e consumo di carta da macero
Per produrre circa 6,8 milioni di tonnellate di carta all'anno - di cui 2,8 di carte per uso grafico - l'industria cartaria italiana consuma circa 3,3 milioni di tonnellate di carta da macero, di cui circa 800.000 tonnellate di giornalame misto.
Oltre 200.000 di queste sono importate, proprio a causa del modesto livello di raccolta interna, con la conseguenza di un più elevato costo del macero utilizzato e di una minore competitività dell'industria cartaria italiana rispetto alla concorrenza internazionale.
In totale un milione di tonnellate di macero è importato nel nostro Paese per produrre carta, mentre oltre 4 milioni di tonnellate di carta e cartone vanno in discarica pur essendo recuperabili.
Alla raccolta delle famiglie si aggiunge quella effettuata direttamente dalle industrie o tramite raccoglitori specializzati nei centri stampa.
Il processo produttivo della carta da macero
Le fasi del processo produttivo delle carte riciclate sono simili a quelle di altre per le quali vengono impiegate materie prime vergini, fatta eccezione per la parte iniziale della preparazione dell'impasto.
In questa fase è fondamentale togliere dai maceri i materiali estranei, chiamati contaminanti, come plastica, vetro, ferro, colle, paraffina, ecc. la cui presenza crea problemi alla produzione e condiziona la qualità.
La pasta dopo la spappolatura passa attraverso una serie di epuratori studiati appositamente per carte da macero.
Il procedimento avviene in più fasi in modo da togliere inizialmente le parti più grossolane e via via le più piccole.
Più il sistema di epurazione è sofisticato e più la qualità del prodotto finito si avvicina a quello di fibra vergine.
Una epurazione accurata è necessaria soprattutto per le carte riciclate da stampa per le quali le esigenze sono maggiori di quelle per altri usi.
Una volta terminato il processo di epurazione la pasta viene immessa sulla tavola piana della macchina continua e prodotta con la stessa tecnica delle altre carte.
Per produrre carte con un sufficiente grado di bianco, partendo da materie prime meno costose, si ricorre alla disinchiostrazione, con la quale è possibile togliere l'inchiostro presente nei maceri.
L'Italia, povera di risorse forestali, ha sviluppato molto la tecnica per l'impiego delle carte da macero nel settore dell'imballaggio e vanta una notevole esperienza e tradizione.
Solo da alcuni anni si producono carte riciclate anche per il settore grafico. L'evoluzione tecnologica e il cambiamento di mentalità dei consumatori hanno favorito lo sviluppo di queste ultime e pur essendo ancora agli inizi i risultati ottenuti sono positivi. Infatti le qualità che si producono sono veramente valide e per alcuni usi possono essere utilizzate in sostituzione di quelle di fibra vergine.
La produzione di carta riciclata non inquina purché le cartiere abbiano attrezzature adeguate per il trattamento sia delle carte da macero che delle acque di scarico e dei residui di lavorazione.
Importante sottolineare, a conferma della ecocompatibilità della produzione delle carte riciclate, che i residui di lavorazione (fanghi) possono essere riutilizzati in più settori: industria laterizi, lavori stradali come sottofondi, per emendanti agricoli.
Per concludere, in un
mondo di "usa e getta" la filosofia di "usa e riusa" trova spazio anche nell'industria della carta e con risultati positivi perché permette la valorizzazione di materiali e prodotti alternativi.
Tipi di carta e grammatura
Con il nome di carta si intende di solito un materiale di peso non superiore ai 150 g per metro quadrato.
I cartoncini vanno da 150 a 300 g per metro quadrato e i cartoni hanno peso superiore a 300 g per metro quadrato.
Generalmente la carta e i cartoncini vengono venduti a peso, per kg; commercialmente il peso è espresso per risma.
La risma equivale a 500 fogli.
i più comuni tipi di carta
carta pelure, da 10/12 g./mq. a 45 g./mq.
utilizzo per moduli a ricalco o posta aerea
carta satinata, da 50 a 150 g./mq. ,resistenza limitata
utilizzo per stampa di libri, opuscoli e riviste
carta e cartoncino patinato da 70 150 g./mq. la carta, fino 300 g./mq. il cartoncino ,la patinata può essere lucida od opaca
utilizzo per qualsiasi stampato, ma sopratutto adatta per la riproduzione di illustrazioni in nero e a colori, ,con qualsiasi sistema di stampa
carta per offset da 70 150 g./mq. la carta e superiore il cartoncino, può essere liscia od operata (ruvida)
usata per qualsiasi stampato con testo ed illustrazioni
carta per rotocalco da 70 130 g./mq. la carta, liscia, morbida e flessibile
utilizzo per la stampa di riviste
cartoni mo, cartoncini
da 150 a 500 g./mq., lisci, operati o colorati
principalmente utilizzati per copertine di volumi, cartelline, depliant o confezioni di ogni tipo.
il calcolo del peso
Per calcolare, ad esempio, il peso per foglio di una carta formato 70xlOO cm da 150 g per mq si moltiplica la larghezza per la lunghezza per il peso e si divide per 10000.
Per ottenere il peso per risma (in kg) si moltiplica il peso del foglio per 5
e lo si divide per 1O.
la fibra
Molto importante è conoscere il senso della fibra della carta, che corre parallelamente al senso di uscita della bobina dalla macchina continua.
Poiché la carta è poi tagliata in fogli, il senso della fibra è segnato, nella fase di imballo, sopra ciascun pacco.
Durante la stampa, il foglio di carta deve essere sistemato in modo che la fibra corra parallelamente al cilindro di stampa, cioè parallela alla parte lunga del foglio, per evitarne piegature.
La carta, inoltre, si piega meglio nel senso della fibra.
Ecco perché, nel libro legato, il senso della fibra della carta deve essere parallelo al dorso.
l'aquisto
La carta può essere ordinata alla cartiera in misure particolari,
in rapporto a determinate esigenze.
Naturalmente ogni cartiera fabbrica la carta su ordinazione solo per quantitativi rilevanti, che vanno da 30 a 50 q.
In questi casi occorre essere molto chiari circa le caratteristiche, il peso, le dimensioni della carta e il senso della fibra.
I cartoni sono invece generalmente venduti a foglio o a pacco.
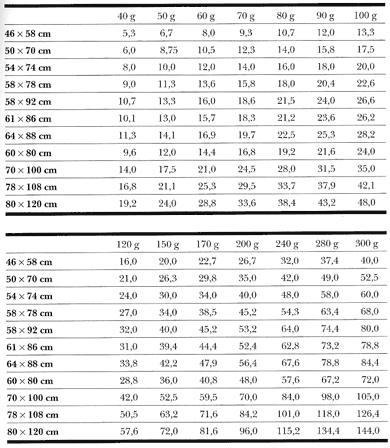
tabella del peso in kg. della carta per risma (500 fogli)
I formati della carta
L'unificazione dei formati secondo le norme UNI (Ente di Unificazione Italiano) comprende tre serie: una fondamentale (A) e due complementari (B e C).
aaaa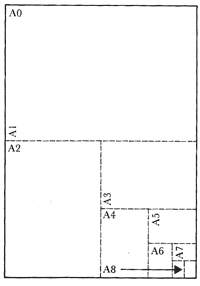
a sinistra,il formato AO comprende la superficie di un mq. (mm.84 X 1189), il lato lungo è uguale alla diagonale del quadrato costruito sul lato corto.
a destra, gli altri formati si ,ottengono dimezzando via via il formato superiore. Nei formati inferiori il lato più lungo è quindi uguale al lato corto del formato superiore.
La serie A fornisce i formati finiti per i più comuni prodotti grafici;
le serie B e C forniscono i formati finiti per prodotti cartotecnici che possono contenere i formati della serie A.
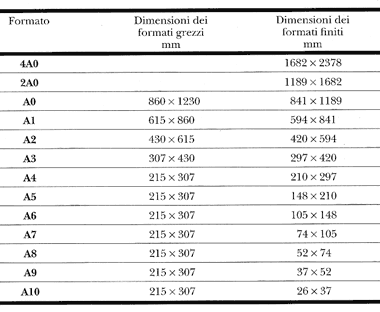
la seire A dei formati UNI dei fogli di carta
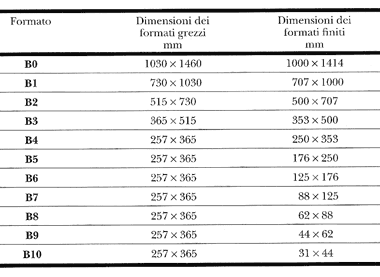
la seire B dei formati UNI dei fogli di carta
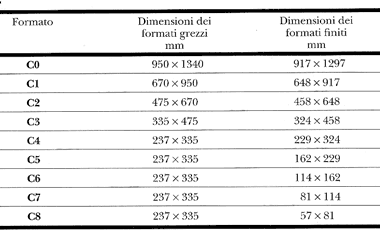
la seire C dei formati UNI dei fogli di carta
I formati finiti sono studiati in modo che, piegando il foglio in due, quattro, sei, otto, sedici ecc. il rapporto fra lato lungo c lato corto resti inalterato.
Inoltre, la lunghezza della diagonale del quadrato costruito sul lato corto corrisponde alla lunghezza del lato lungo.
Per la serie A il formato base (841xl189 mm, AO) corrisponde a l metro quadrato.
Per indicare i formati si usano i simboli delle varie serie (A, B, C) che vengono fatti seguire da un numero che indica quante volte il formato base è stato piegato per ottenere il formato voluto: per esempio, il formato A4 deriva dal formato piegato 4 volte.
Il formato A4 (210x297 mm è particolarmente usato per gli stampati commerciali, carte da lettere, moduli, tabelle e per cataloghi. riviste, monografie.
L'uso di formati normalizzati è particolarmente consigliabile in quanto essi sono in stretta relazione con tutta una serie di normalizzazioni.
